Work Experience
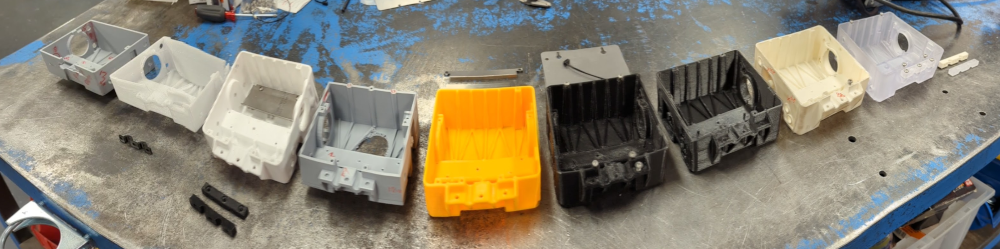
Research/Product Development Engineer LR Dynamics | 2020-Present
Currently a Product Development and R&D Engineer working on winches and safety straps for gymnasium/stage applications.
- Developed product improvements across existing products through design changes, process improvements, material reductions, and alternative component selection.
- Worked directly with on-site manufacturing and assembly groups to develop process and product improvements across the company - implementing Lean 5S, 8 wastes, and Shingo principles.
- Used SolidWorks to design: sheet metal, laser cut, machined, and plastic injection molded parts.
- Implemented GD&T on multiple preexisting cast and machined parts to improve quality.
- Rapid prototyping using FDM and SLA 3D printing to validate designs.
- Implemented SolidWorks PDM and created an ECO process for version control and history tracking.
- Performed over a dozen immediate cost reduction focused improvement projects with saving up to 50% in material and process costs and moved multiple manufacturing processes to internal or domestic suppliers.
- Completed a 16-month-long project to change a component from a bent/welded sheet metal part to a plastic injection molded part saving $150k annually as well as reducing assembly time by half.
- Moved injection molded components to 3D printing saving 90% ($6.27 to $0.61) on multiple parts.
- Improved assembly line processes by creating an automated end-of-assembly-line tester, doubling throughput and moving to one-piece flow to further improve overall productivity.
- Worked on a team to design multiple test fixtures from small key-switch cycle testing to a 20’ tall electric winch cycle tester using Arduinos and Siemens PLCs for automation.
Project Engineer FLSmidth | 2018-2020
Worked as a Project Engineer for milling equipment for mining.
- Mechanical and Project Engineer on 6 major Engineer-to-Order (ETO) projects for 12 Ball and SAG mills as well as dozens of smaller wear-part and R&D projects worldwide.
- Primarily work in SolidWorks to create new models, large mechanical assemblies, and drawings with Enovia (PDM) usage for document control.
- Part of an engineering R&D team developing new mill sealing arrangements using Polyurethane components that have been installed and revised across multiple mills - success has led to further R&D projects in the same area.
- Interact daily with clients, project managers, other engineering groups, sub-suppliers, senior engineers, and multiple drafting teams to ensure efficient year long project execution and delivery of over 100 engineering documents each.
- Support sales and customer support teams to answer technical questions and create proposals.
- Evaluate international standards against internal design standards to ensure designs meet project requirements.
- Create engineering schedules and identify issues early to ensure project commitments are met.
- Monitor engineering budget use and issue Engineering Change Orders (ECO) outlining costs and project impacts.
- Resolve manufacturing and installation issues with tracking through detailed Non-Conformance Reports (NCR).
- Complete reviews of all detail drawings, assemblies, parts lists, piping and instrumentation diagrams (P&ID/C&ID), and tools needed for installation and commissioning before release.
- Prepare general engineering calculations and reports using SolidWorks, Mathcad, and Excel.
- Work primarily in SolidWorks and Enovia PDM with minor AutoCAD 2D Mechanical work – other software includes Microsoft Office (Excel, Word, Outlook), Microsoft Teams, Skype.
Design Engineer Intern Ovivo | 2018
Designed municiple water clarifiers and thickeners, and assisted with retrofitting equipment to exisiting systems.
- Primarily work in Autodesk Inventor 3D CAD software – experience using parametric modeling, working with large assemblies, sheet metal, bolted connections, and frame generator, drafting, parts list generation, and GD&T.
- Design and create new 3D models for large municipal water clarifier assemblies including truss and beam walkways, walkway platforms, piping, truss rake arms, skimmers, and center cages.
- Correct and redesign existing 3D models while maintaining existing relationships and parametric dimensions.
- Create detailed mechanical assemblies and part drawing packages for large water clarifier tank mechanisms.
- Worked with overseas drafting teams to consistently reduce the time it took to complete project drawing packages from approximately 3 weeks to 1 week by implementing drafting training sessions.
- Select, design and prepare fasteners lists and Bills of Materials (BOM) for large assemblies.
- Experience using Autodesk Vault (PDM) to create Engineering Change Orders (ECOs) to control releases and revisions.
- Work with fabricators and customers to meet design specifications and answer questions in a timely manner.
- Visit customer facilities to assist with structural inspections, measuring, and assembly of clarifiers.
Engineer Intern Colmek | 2017-2018
Worked with engineers to develop AS9102 inspection procedures and testing for rugged military electrical systems.
- Assisted with initial product conception and design ideas.
- Researched regulations and standards for military applications.
- Written detailed manufacturing instructions for several navy computer systems manufactured by Colmek.
- Written and executed engineering change orders(ECOs) when needed.
- Created mechanical drawings from CAD models using SolidWorks.
- Updated existing CAD models using SolidWorks.
- Written usage and specification manuals for Colmek's Thermite rugged computer systems.
- Tested and documented performance of computer and power systems before shipping.
- Troubleshot and repaired various electrical systems either from RMAs or failure during initial testing.
- Performed cost analysis on RMAs and maintenance procedures as well as identified any EOL or difficult to find components.
- Created detailed Aerospace Standard First Article Inspection Reports (FAIRs) in compliance with AS9102:
- Review all assembly components and Bill of Materials (BOMs) for accuracy.
- Check all components for valid Certificates of Conformance (CofCs) from manufacturers.
- Verify that all measurements and other values listed on drawings are within tolerances.